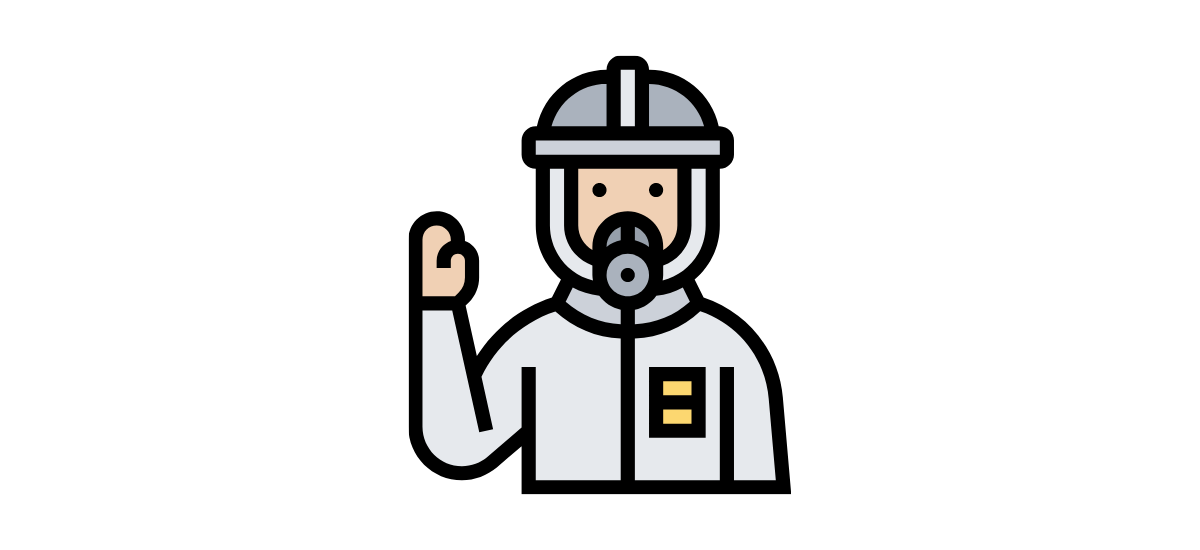
Contamination control is the general term given to the process of eliminating and preventing contamination on surfaces and in the atmosphere. In a laboratory environment, adhering to proper contamination control guidelines helps to keep staff and the facility safe, and helps to prevent cross-contamination during the process of testing.
Depending on the nature of the work done in your facility, you may need to include a number of daily cleaning and contamination control procedures to ensure your facility remains safe and productive. At OnePointe Solutions, our furniture is always built with the specific needs of your facility in mind.
For many of our clients, the ability to quickly and efficiently sanitize surfaces, remove airborne pollutants, and avoid cross-contamination or degradation of test results is paramount to the success of their work. To facilitate the needs of our clients, we offer a number of contamination control features and help our clients to design with cleanliness and safety in mind.
Contamination Control Solutions
Optimizing your laboratory contamination control can begin from the moment you start designing your laboratory. Many of our pharmaceutical and medical clients choose us specifically for our expertise in the world of cleanroom design, and for the number of high-quality surface materials we offer that make cleaning up at the end of the day fast and easy.
Here are a few of our products and services that can help you optimize your laboratory contamination control:
Cleanroom Design
Cleanrooms are designed to specifically minimize the presence of foreign and unwanted particles during the experimentation and manufacturing of pharmaceuticals. Cleanrooms are essentially laboratories that are optimized for pharmaceutical contamination control. When you choose OnePointe Solutions to help build your cleanroom or pharmaceutical laboratory, we’ll help you evaluate every part of your facility and design.
When we visit your location (our team will travel anywhere in the U.S.), we’ll evaluate your environmental location, the laboratory facility itself and its construction, your storage and furniture needs, and your special equipment needs like mass spectrometers, fume hoods, specialized waste management systems, and so on. We also have a full line of cleanroom seating, so your staff can work comfortably without compromising cleanliness or safety. Once our team has had a chance to take a look at your facility, we will create custom 3D renderings, and create a quote so you can get an almost immediate look at the future design of your lab.
Fume Hoods and Biosafety Cabinets
Fume hoods and biosafety cabinets provide vital filtration for laboratory facilities handling hazardous chemicals, infectious diseases, or toxic agents that have the potential to become airborne. Fume hoods draw airborne pollutants and toxins away from personnel and the workspace, filtering out contaminants before recirculating air within the facility. These instruments help to prevent personnel from contracting airborne illnesses, inhaling irritants, or inhaling potentially toxic chemicals.
To accommodate the needs of laboratories with a variety of filtration and ventilation needs, we offer a number of fume hood options:
- General chemistry hoods
- Biosafety hoods
- Educational demonstration hoods
- Ductless/filtered hoods
- Floor-mounted hoods
- PVC and stainless hoods
- Steam, heat, and light vapor hoods
- Ventilated mass spect enclosures
- Ventilated casework and refrigeration units
Anti-Microbial Furniture
Though all of the worksurface materials offered here at OnePointe Solutions are designed to be easy to clean, some are made specifically to prevent the spread of bacteria or illnesses. Our anti-microbial furniture is finished with a special coating that kills infectious agents and prevents the buildup of bacteria. Anti-microbial casework and worksurfaces are ideal for pharmaceutical labs, clinical labs, animal research facilities, and cleanrooms.
Personnel Contamination Control
Labs handling toxic materials or infectious agents should take special care to prevent environmental contamination due to improper personnel cleanliness. A vital contamination control consideration, BSL-3 and BSL-4 labs should implement the use of personal protective equipment, handwash stations, and shower stations where necessary. Within the facility, personnel should practice regular handwashing and surface sanitation procedures, and should always use best practices when handling toxic chemicals or potentially harmful agents.
Surface Cleanliness
One of the most important -though often overlooked- contamination control procedures is to properly clean your worksurfaces. Most laboratory work surfaces, even those that do not come in direct contact with chemicals or sample materials, require weekly if not daily cleanings. Though intuition can get you relatively far when you clean your worksurfaces, knowing how to clean your specific worksurfaces is important to ensure the longevity of your lab furniture.
At OnePointe Solutions, we offer a variety of worksurface materials, like epoxy resin, stainless steel, maple block, and more. Each surface material has its own unique attributes, with some better suited for certain tasks than others. Wood and maple block, for example, will be less resistant to water, moisture, and particle buildup than surface materials like stainless steel or phenolic resin. Not sure what surface material might be right for your laboratory? Check out our guide covering how to choose the right work surface.
Need Help Figuring Out Contamination Controls for Your Lab?
Our lab design team at OnePointe Solutions can help you figure out designs and furniture needed to make sure contamination controls in your lab adhere to proper guidelines. Give us a call at (866) 222-79494 for a free quote to get started.