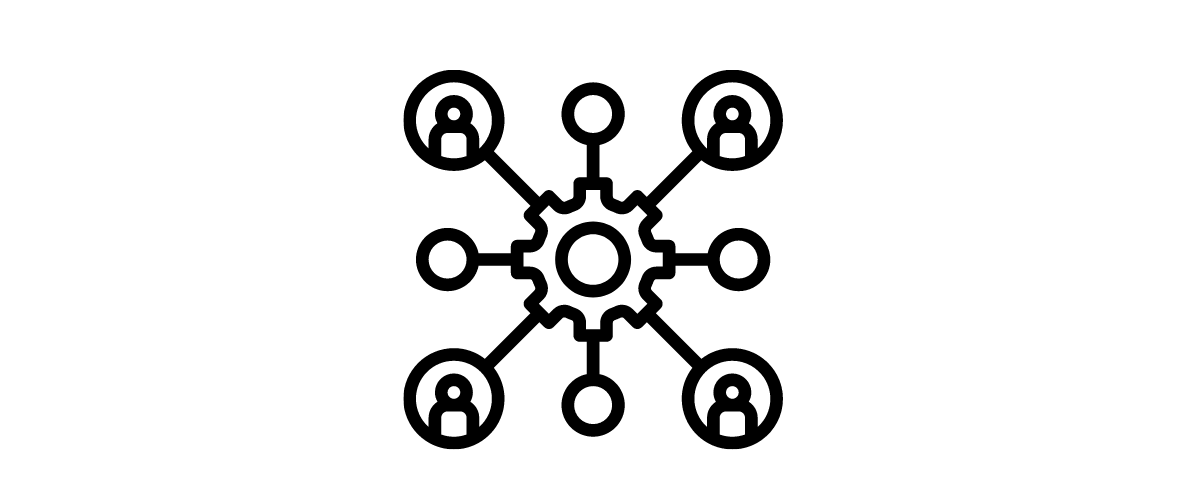
Labs around the world come in all shapes, sizes, and layouts, but while many design elements are entirely up to personal preference, there are some considerations all good planners make when creating an optimized laboratory design.
Labs provide the high-tech environment in which educators and researchers uncover incredible discoveries, develop life-altering medicines, and educate the world’s future doctors, researchers, and scientific minds. To facilitate the work being done in the lab, lab designers work to custom build facilities that optimize workflow, support researcher needs, and enhance safety.
Spending additional time to make clear, well thought out decisions during the initial design process can help you to avoid running into issues down the line. Some novice designers and lab managers mistakenly believe that they can make any space work, or that they can go over just the basics before making final decisions. Without fully considering the needs of your researchers and the specific rhythm of their workflow, you could end up creating a space that inhibits rather than helps support the scientific process.
At OnePointe Solutions, we specialize in designing, building, and installing custom laboratory furniture, and have worked with countless researchers, designers, and experts to discover what it takes to create the perfect laboratory solutions. In the course of our work, we’ve learned the key to optimizing a laboratory layout, and are here to share a few tips, tricks, and pieces of advice to help you do just that:
Pre-Planning On-Site
Before you begin any project, the first step should always be to visit the site in person in order to map out and conceptualize what the final results should look like. At OnePointe Solutions, our design team begins every project by personally visiting the client’s facility in order to get a good, in-person look at the space. A detailed walkthrough of the space will provide a general overview of layout possibilities, can give designers a better understanding of the constraints of the facility, and can spark creative solutions that might not have appeared on paper.
Utility Layout Assessment
During an onsite visit, a designer will identify where in the building or on the construction site utilities will be positioned, which will impact the final design of the laboratory layout. Scientists, researchers, and technicians will need to access utilities like HVAC, water, heating, gas, trash, and other important amenities, so the final design should account for utilities that are already present. If the lab is being built in an already existing structure, a comprehensive list of utilities and a map detailing where each can be accessed will help during the design process.
Access
Along with utility access, it is important to determine whether the space you are designing will provide adequate access to other areas of the building, storage, emergency exits, deliveries, etc. Some educational labs may be able to be located anywhere in a building, whereas research facilities for major corporations or pharmaceutical companies may prefer to be located on the bottom floor closest to emergency exits, or may need special access to delivery/entrance areas.
Meet with Researchers & Stakeholders
While a designer may be able to create a usable lab that could work for a variety of purposes, creating a custom, optimized lab requires a more intimate understanding of the work to be done within the facility. Before beginning the designing process, designers should meet with all stakeholders and facility researchers to determine the specific needs of the team. The lab needs to be tailored to the workflow of its users, so bringing in the research team or staff to consult before the building even begins can help you to identify key issues or areas to focus on.
In specific types of research, materials and samples must be kept in carefully controlled and isolated environments in order to preserve the integrity of test results and produce the purest products possible. Meeting with team researchers will help the designer to fully understand how different areas of the lab need to interact, and can help to give a clearer picture of what areas will be the most critical.
List Equipment & Materials
Some labs with different departments or areas choose to consolidate their equipment and consumable materials (i.e. gas, washing stations) in one centralized area of the lab, whereas others choose to spread them out, providing individual utilities and tools for each department. Making a comprehensive list of all equipment, materials, and consumables used by each department will help you to determine whether you will need to allow space for each to have its own separate equipment and materials, or whether you can combine for efficiency.
Making a full list of equipment will also help to show whether you have chosen an area with enough space to accommodate all necessary items, or can show you where you may need to expand, adjust, cut back, or revise your designs entirely. Neglecting to account for all necessary equipment before you begin building your lab could result in cramped, uncomfortable working conditions which could interfere with the efficiency and workflow of your lab. Remember, approximately a quarter of your lab space will eventually be taken up by large equipment, so it is vital that you ensure you have adequate space for all necessary items.
Account for Storage
While some consumables and important pieces of equipment may remain on the workroom floor, many other instruments, tools, and chemicals will need to be stored in safe, climate-controlled storage areas that are easily accessible by lab personnel. Chemical storage should be nearby to avoid contamination and to improve efficiency but should be kept separate from any area of the lab where open flame, high heat, corrosive chemicals, or other hazardous materials are in active use. Remember, your inventory will only increase over time, so include more space than you think is necessary in your lab design.
Design for Flexibility
While some educational labs remain the same for years, most research and industrial facilities change the work they do and how they do it frequently. A lab may go from sequencing DNA to testing food products in just a few months and must be able to make the transition from one to the other without needing a full remodel. Flexible, easily modified labs are more successful and lucrative than those built for permanence since flexible labs will be able to keep up with changing needs, techniques, and workflow.
Designing with flexibility in mind is also helpful for the natural expansion of any operation, since you will likely bring on new/more team members over time, increase inventory, and shift operations as you become more experienced.
Modular Furniture
One of the easiest ways to increase the flexibility of your laboratory is to include modular furniture in your design. At OnePointe Solutions, many of our laboratory furniture options include modular features and add-ons that make them readily adaptable to changes in your facility. Items like our lab islands include adjustable height options, flexible/modular shelving, and locking or rolling casters for easy reconfiguration of the space.
Open vs. Closed Lab Design
In the past, lab designers opted to section off labs, creating smaller rooms/areas for individual researchers to work in in private. While this approach to lab design can be executed successfully, modern lab designers have begun to opt instead for an open concept design, no longer sequestering researchers and technicians from one another, and instead creating a more collaborative working environment. In addition to being a more social, more natural environment to work in, open concept labs also allow for additional flexibility with the absence of walls and barriers to reconfigurations.
Consider Comfort
The most efficient workplaces are those that take the comfort of their staff into consideration. Comfortable seating and ergonomic furniture designed to maximize support, improve posture, and relieve tension are just one example of a design eliminate that can increase staff comfort and, consequently, productivity. Similarly, supplying adequate natural and artificial lighting is an important feature to prevent eye strain, maintain staff alertness, and minimize workplace accidents. During the design process, be sure to include plenty of windows, and to build in high-quality artificial and supplementary lighting wherever necessary.
Safety First
During all stages of the design process, it is important to consider the safety of all members of staff, the facility, and the materials/equipment in the lab. Fume hoods, biosafety cabinets, eyewash stations, fire-extinguishers, and other safety equipment should be placed strategically throughout the lab, and made available in adequate supply for all members of the team to have equal and ready access in case of emergency.
Building Security
As important as safety within the lab is, it is equally important to ensure the lab itself and the facility as a whole is kept secure. In some labs, techs and researchers may be handling sensitive materials or private information not available for public viewing or research. Additional levels of security and access limitations preventing non-essential individuals from entering the private lab areas may be necessary, and should be considered during the design process.
Creating built-in security systems to prevent non-personnel from entering the lab is both to protect the safety of individuals and materials inside, and to create a focused environment in which researchers can complete their work. Privacy and a sense of security are key ingredients for focus and can help to keep work on schedule.
Need help optimizing your lab?
Call us today (866) 612-7312 to speak to one of our lab planners to walk you through the process and to discuss any other questions you have when it comes to your lab.